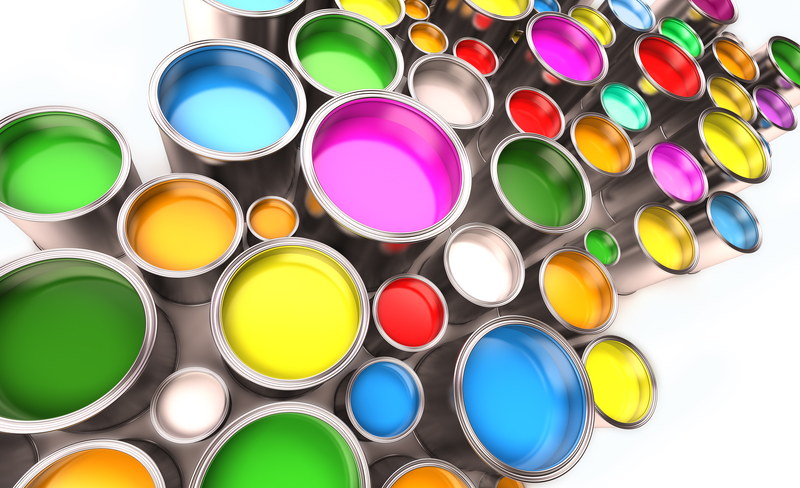
Coatings have been around since ancient times by using sap, berry juices and eggs. In 1880, Sherwin Williams produced the first gallon of premixed paint and since then the industry has been growing into a multibillion-dollar industry. The main markets for coatings are architectural, automotive, marine, industrial and specialty. Within these markets the typical coating is made up of resins, solvents, pigments, and additives. Below is a reference guide on what each component does to help successfully create a coating.
- Resins are used for their film properties that help to bind together the pigments.
- Solvents are used to help with the application ease as it will help disperse the other components into the formulation to create a smooth product.
- Pigments are used for color of the coatings but can also help with gloss control and corrosion inhabitation. These are usually higher in cost depending on which ones are used but they can act as a filler for the coating to help reduce overall costs.
- Additives are used to help change the appearance, quality, and durability of the coatings.
Typical Formulation for Coatings:
Resins: | 40-45% |
Pigments/Fillers: | 30-32% |
Solvents: | 20% |
Additives: | 4-5% |
ChemCeed Products That Go into Coatings:
- Epoxy Resins
- Toluene
- VM&P Naphtha
- Mineral Spirits
- Glycol Ethers
- Titanium Dioxide (rutile and anatase)
- Carbon Black
- Zinc Oxide
- Color Dyes and Dispersions
- Plasticizers
- Flame retardants
- Defoamers
- Corrosion inhibitors
Processing Steps:
- Mixing: resins, pigments, fillers, and plasticizers are put into a mixer
- Grinding: after mixing the mixture is transferred to mills to help create a smoother product.
- Thinning/dilution: solvents and other additives are added into mixture and mixed.
- Filtration/Finishing: The mixture is filtered to remove any sediment.
Packaging and Storage: Mixture is poured into totes, drums, cans, pails, etc. then labeled and goes into storage for sale.